Operational Excellence
In fiscal 2024, ADS spent over $15 million in capital projects related to environmental, health and safety projects to mitigate risk across our manufacturing and logistics network. We’re focused on automating as much work as possible in downstream manufacturing processes, where we face our greatest safety challenges. Our operations follow a comprehensive, proactive safety and health management system that includes a collaborative process to prevent, find and fix workplace hazards prior to injury occurrence.
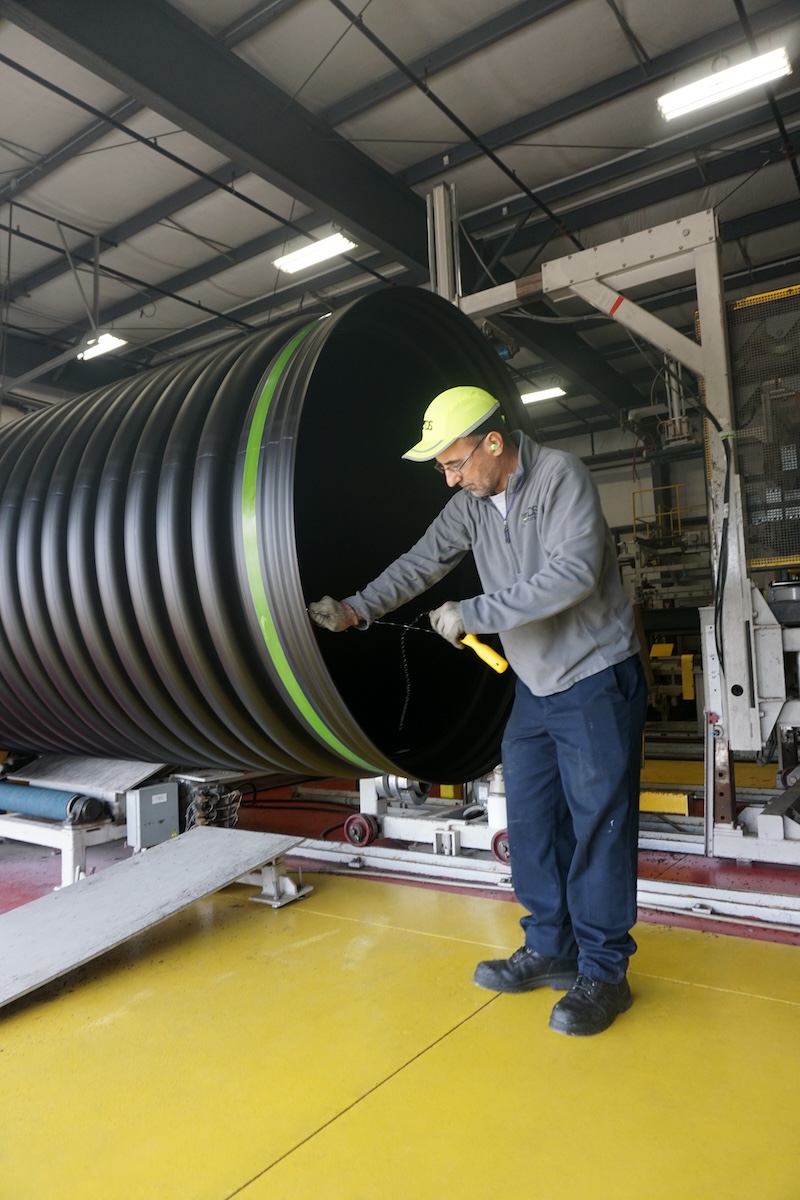
Safety Training
ADS continues to build on a robust program of employee safety training:
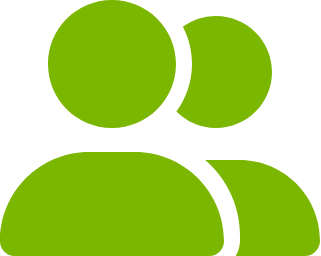
New hires
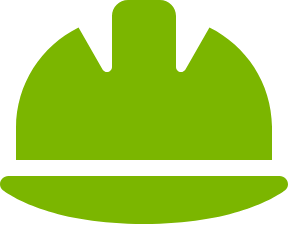
Shift and plant supervisors
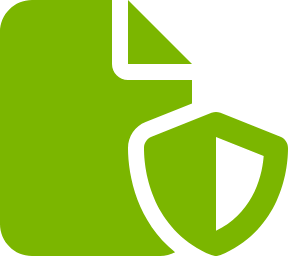
Fleet safety
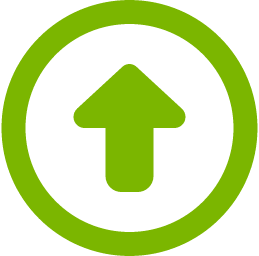
Results
Employee Health and Safety 17, 18 | Fiscal 2022 | Fiscal 2023 | Fiscal 2024 |
---|---|---|---|
Total Recordable Injury Rate 19 | 2.7 | 2.6 | 2.1 |
- Safety statistics are representative of the ADS Legacy operations in the United States and Canada and Infiltrator. Jet Polymers and Cultec data is included starting in Fiscal 2023. The data does not include joint ventures in Mexico or Other International, which represent less than 5% of net sales.
- Rates are calculated as: (Statistic count x 200,000) / hours worked.
- TRIR: A work-related injury or illness is considered a recordable incident if it results in any of the following: death, days away from work, restricted work or transfer to another job, medical treatment beyond first aid, or loss of consciousness. Additionally, a significant injury or illness diagnosed by a physician or other licensed health care professional is considered a recordable incident, even if it does not result in death, days away from work, restricted work or job transfer, medical treatment beyond first aid, or loss of consciousness.
Operation Clean Sweep
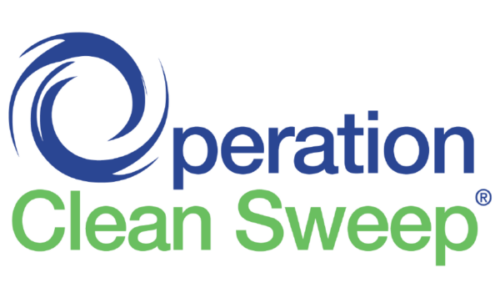
Keeping plastic waste out of the environment is critical to our commitment to sustainability and environmental protection. That’s why we are a leading member of Operation Clean Sweep, a joint initiative of the American Chemistry Council and the Plastics Industry Association aiming for zero loss of plastic resin pellets into the environment.
ADS is a blue level OCS member, meaning we adhere to the strictest standards for preventing pellet loss and auditing our success.
Strategies include concrete berms and filters on stormwater basins to catch plastic as well as custom pans to capture any spillover from rail cars. Three times each shift, crews inspect the transfer points for pellets to be sure they’re tight. Crew members wear backpack vacuums to enable instant cleanup of any pellet spills.
Closing the Loop on Water
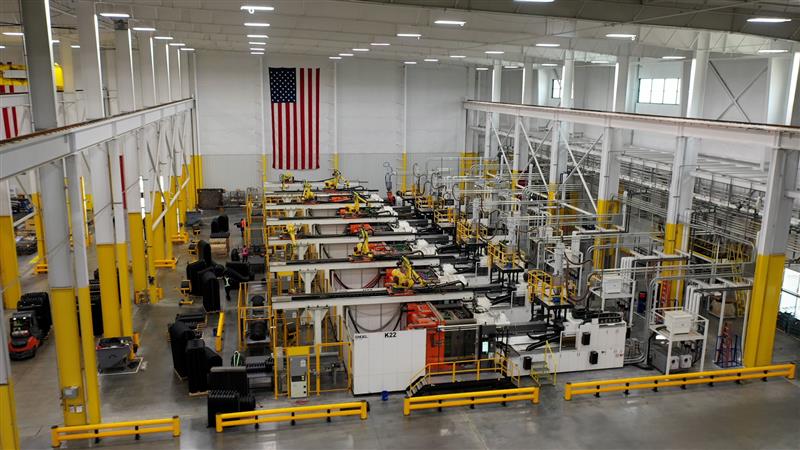
Our mission of protecting water isn’t only about our drainage systems. Water scarcity is one of the defining issues of the 21st century, and we are focused on reducing our water consumption during the manufacturing process by implementing closed-loop systems to reuse water multiple times for cooling purposes before discharging it.
100% of the legacy ADS pipe manufacturing facilities utilize closed loop water systems. We are currently evaluating the remaining manufacturing sites to evaluate the feasibility of utilizing closed loop water systems.